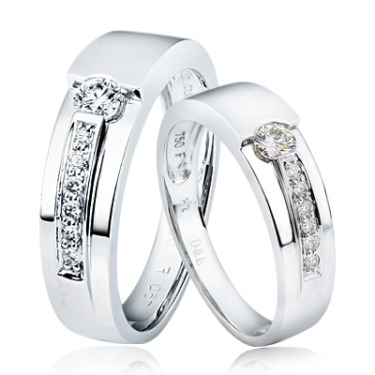
1. Marking (dashing): This is the first step in diamond cutting. The first step is to inspect the rough and mark the surface of the diamond. The person who does this work has extensive experience and is proficient in processing technology. The ultimate goal is to create the largest, cleanest and most perfect diamonds to reflect the value of the diamond as high as possible. The liner must pay attention to two points: that is, try to keep the maximum weight while minimizing the contents. The liner uses a magnifying glass to study the structure of the drill blank. If it is a large-grained diamond, this work may take several months, and it takes a few minutes for a common rough diamond. However, no matter how small the rough diamonds are, each diamond undergoes detailed inspection to make a correct judgment.
The liner used Indian ink to mark the rough blank, showing that the rough blank should be divided along this line. It is usually streaked along the natural texture of the diamond as much as possible.
2. Dividing the original stone: including cutting and sawing.
Castration: The stinger places the drilled blank of the marked line on the frame, then cuts another dent along the dividing line, and then puts the square edge knife on the dent, handcuffed on the rake. When the knife strikes with the right force, the diamond will be split into two or more pieces along the grain direction.
Sawing: Most diamonds are not suitable for splitting and need to be sawed. Since only diamonds can cut diamonds, the saw blade is a phosphor bronze wafer coated with diamond powder and lubricant on the edge. The diamond is fixed on the clamp and the saw blade is rotated at a high speed to saw the diamond. Modern laser technology introduces diamond cutting, greatly improving the machining efficiency of rough diamonds.
Forming: The sawed or split diamonds are sent to the rounding department for rounding and forming, that is, according to the design requirements, the diamonds are made into round, heart-shaped, elliptical, cusp-shaped, emerald-shaped and other common cut flower shapes. Or other special shapes. Since diamonds are the hardest natural substances humans have ever known, only diamonds can polish diamonds, and because diamonds have slightly different hardness in all directions. Therefore, with the experience of grinding, grasp the basic shape of the diamond: trigonal, octahedral, dodecahedron and crystal characteristics. The general method is to drill the billet on a lathe that rotates at a high speed, and then use the diamond on the other arm to round the rotating billet.
3. Beginning and polishing: On a cast iron disc coated with diamond powder and lubricating oil, the car grinds all petal surfaces (facets), giving the diamond an attractive brilliance. The process of grinding is usually to make 8 large surfaces at the bottom and then 16 facets. With a sharp bottom, a total of 25 facets were correctly corrected, and this extended the triangular facet, the kite face, and the facet on the waist, with a total of 33 facets, so that a total of 58 facets of a round diamond, If there are no bottom facets, there are 57 facets.
Not every rough diamond must go through all the above steps. This depends on the characteristics of the rough diamond itself and the objectives to be attained. For example, the above “flat†rough diamond may not need to cut this process. Machining emerald diamonds does not require a "round-up" process. However, there are two processes that are indispensable for any diamond blank. This is "dashing," "flapping, polishing." The position and angle of a petal produced by a Seiko-cut diamond are precisely calculated to give the diamond its maximum brilliance. It can thus be seen that cutting the world’s hardest gemstone, the diamond, not only requires advanced equipment, but also requires that the division’s experienced experience, high sense of responsibility, and engrossed attention in order to release all the diamond's spiritual colors. A diamond in the jewellery counter may have survived many countries, and after a few people's hands, it becomes a diamond jewelry after processing, inlaying, and making. With the advancement of science and technology, the introduction of laser technology and electronic computer descriptions can make the design and cutting of drill blanks more accurate.
Infinity Sterling Silver Jewellery,Cheapest Opal Ruby Earrings,Stud Earrings,Kingdom Hearts Ring
Rings,Jewelry Co., Ltd. , http://www.baoli-jewelry.com